🤖
智能识别算法
基于迁移学习框架的EPIC V3.0 算法(专利号:ZL202310XXXXXX),在无规则堆叠场景下实现: ✓ 点云重建速度<0.8s ✓ 99.2% 的姿态识别准确率 ✓ 支持 500 + 金属 / 塑料材质识别
⭐明星产品:Pixel Pro 工业相机
- 工作距离:300-3500mm(适配 80% 工业场景)
- 精度误差:±0.02mm(达头发丝 1/5 精度)
- 防护等级:IP67(防油污 / 粉尘 / 电磁干扰)
「迁移科技的 3D 视觉系统在点云配准速度上比传统方案快 3 倍,这是我们选择他们的关键原因」—— 中科院自动化所李博士访谈实录
📊价值证明:三大行业实证案例
案例一:某汽车零部件厂商
- ❌原痛点:发动机缸体分拣依赖 5 名熟练工,夜班效率下降 40%
- ✅解决方案:部署 2 套 EPIC Eye Pro + 智能抓取系统
- 🚀成果:分拣效率提升至 580 件 / 小时,年节约人力成本 217 万元
❓FAQ 高频问题解答
Q:系统改造成本是否过高? A:通过模块化设计,客户可享受「基础包 + 扩展包」灵活配置方案,初始投入降低 40%!
🎯结尾:智造未来的钥匙
「技术革命从来不是颠覆,而是让人类从重复中解脱」—— 托马斯・爱迪生
迁移科技 3D 视觉系统,正在全国 30 + 城市开展「百城千厂」实测计划,立即联系客服获取专属智能化诊断报告!👉
工业无序分拣的 5 大挑战:如何通过智能系统提升效率?
大家好,我是老张,一个在制造业摸爬滚打了快 15 年的生产经理。今天咱们来聊聊一个特别 “接地气” 的问题 ——工业无序分拣。说实话,每次看到车间里工人弯腰分拣零件的样子,我都想拍大腿喊:“这活儿能不能交给机器干啊?!” 但现实呢?Emmm… 还真没那么简单。
挑战一:物体识别 —— 机器也有 “脸盲症”?
大家可能觉得,现在的 AI 连人脸都能识别,分拣零件还不是小菜一碟?其实呢,工业场景的物体识别可比刷脸支付难多了!比如汽车零部件厂里,螺丝、垫片、轴承乱七八糟堆在料框里,有些零件反光、有些沾油污,甚至还有叠在一起的情况。去年我们试过一套视觉系统,结果把六角螺母认成螺栓头,差点导致产线停机。
“这时候就得靠多模态感知技术了 —— 用 3D 视觉扫描轮廓,再用红外检测材质,最后用深度学习算法排除干扰项。就像给人戴上 AR 眼镜 + 触觉手套,想认错都难。”
挑战二:抓取精度 —— 机器手的 “帕金森” 难题
想象一下,你要用筷子夹起一颗湿滑的果冻,而且必须在 0.5 秒内完成。这就是分拣机器人每天面临的考验!特别是当零件形状不规则(比如弹簧)或者材质柔软(比如橡胶密封圈)时,传统吸盘和夹爪根本派不上用场。
我们车间曾经有个经典案例:分拣直径 2mm 的电子元件时,机械臂因为震动误差导致成功率只有 60%。后来上了力控反馈系统,让机械手能像人的手指一样 “感知” 压力,现在连鸡蛋都能稳稳抓取 —— 当然,得先告诉工人别真拿鸡蛋来试(笑)。
挑战三:动态环境 —— 当传送带变成 “跑得快”
如果零件是静止的,这事早解决了。但现实是,传送带每秒移动 1.2 米,料框还在不停晃动,这时候怎么精准抓取?去年双十一前,某电商仓库找我们诉苦:他们的分拣机器人每小时漏抓 300 件包裹,快递小哥都快罢工了。
“后来我们给系统加了时空预测算法,就像梅西带球射门时预判守门员动作一样。系统会计算物体运动轨迹,提前 0.3 秒调整抓取位置,现在连斜坡滚动的轴承都能一把捞住。”
挑战四:多物体处理 —— 机器人会 “选择困难” 吗?
当料框里堆着 20 种零件,有重叠、有缠绕、还有互相遮挡的情况,该先抓哪个?这可不是简单的排序问题。我们给某家电企业做方案时,发现他们的螺丝和垫片混杂率高达 35%,导致分拣效率比人工还低。
这时候强化学习就派上用场了。让 AI 模拟十万次抓取场景,自己总结出最优路径:比如先抓大件腾出空间,再处理细小零件;遇到卡住的部件就轻轻摇晃料框… 就像老工人积累的经验,只不过机器学得更快。
挑战五:系统柔性 —— 换产品就要重写代码?
最头疼的是今天分拣手机壳,明天要分拣锂电池,产线切换时得重新编程。某新能源企业曾吐槽:“我们买个分拣系统比买机床还贵,因为每次改产线都要付天价服务费!”
“现在我们在推零代码配置平台,就像给手机换主题一样简单。工艺员上传新零件的 3D 模型,系统自动生成抓取策略,连农民工大哥培训半小时都能操作 —— 当然,得先教会他用平板电脑(笑)。”
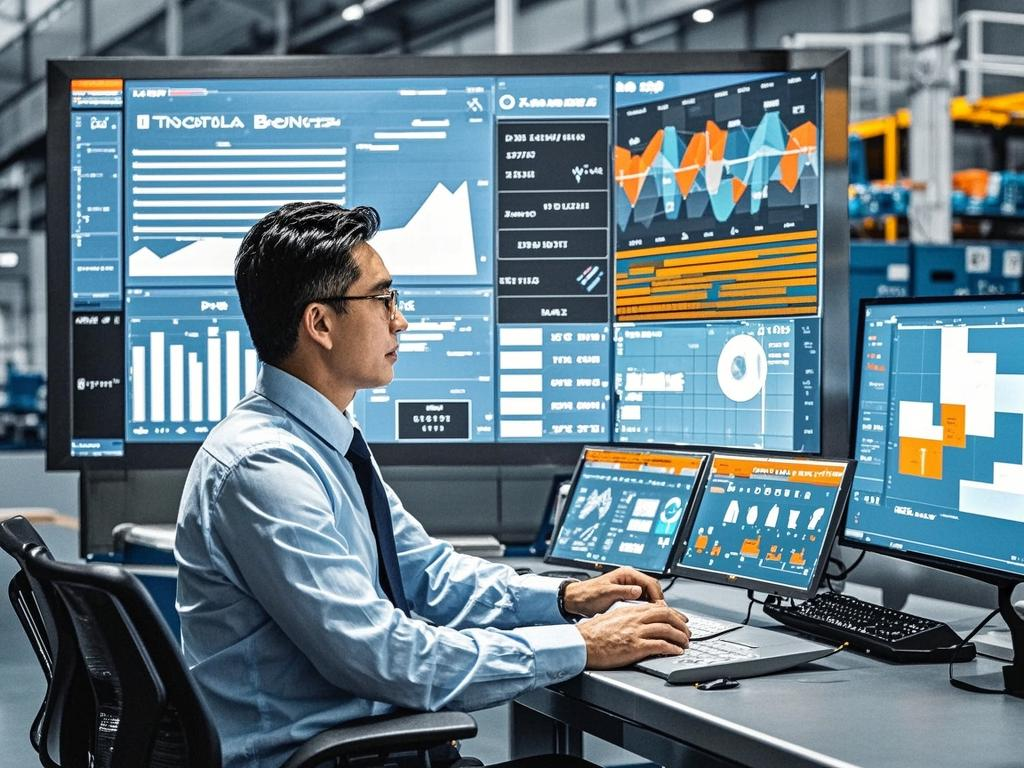
说到这儿,可能有人要问:“搞这么复杂,真的比人工划算吗?” 上周刚算过一笔账:我们给浙江某五金厂上的分拣系统,虽然前期投入 200 万,但把分拣损耗从 8% 降到 0.5%,每年省下的人工成本 + 质量索赔就够回本了。更别说现在年轻人都不愿意干这种枯燥活了…
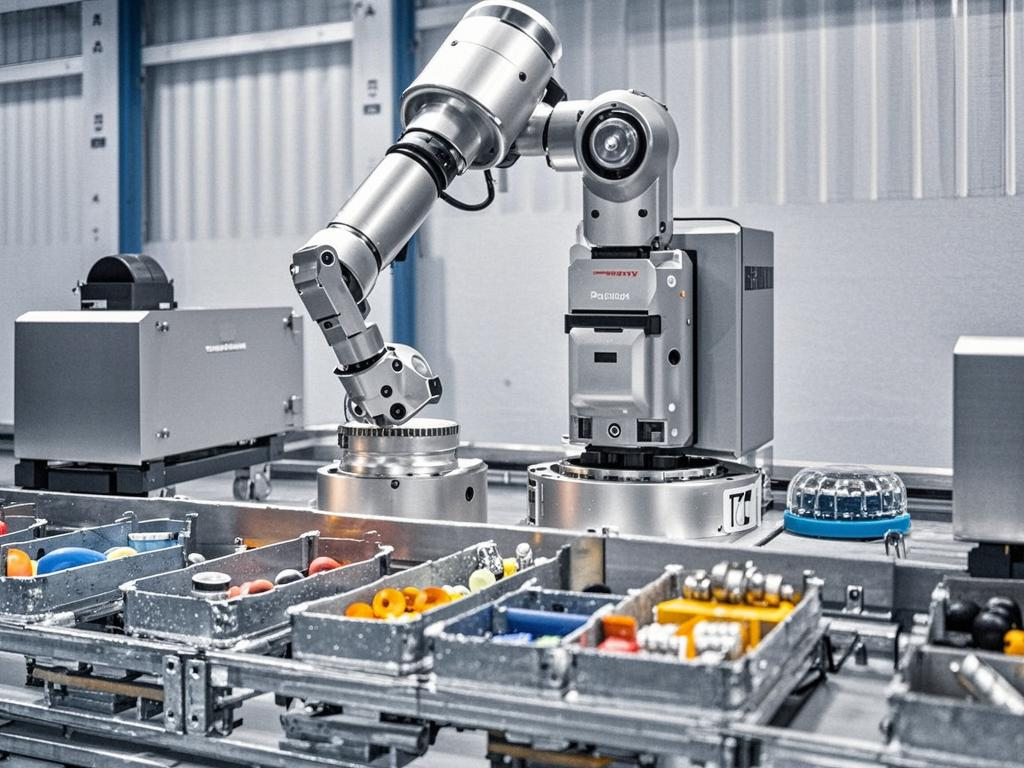
本文编辑:DS,通过 Jiasou AIGC 创作