📌 核心摘要
在工业 4.0 转型浪潮中,迁移科技通过自主研发的3D 视觉系统已为汽车、家电、物流等 12 个行业提供智能化解决方案。搭载 DL 算法的 Epic Eye 系列工业相机实现 ±0.05mm 测量精度,2024 新品 Pixel Pro 更将处理速度提升至3.6 秒 / 件。本文基于 300 + 落地案例实测数据,深度解析机械臂应用中的定位偏差、柔性适配、环境干扰三大核心痛点解决方案。
⚠️ 行业痛点深度扫描
🎯 某汽车零部件厂焊接车间 ▸ 传统示教模式需2.5 小时 / 产线调试 ▸ 工件反光导致15% 废品率 (数据来源:GGII《2024 工业机器人白皮书》)
行业 |
平均停机率 |
定位误差>1mm |
家电制造 |
22% |
38% |
汽车焊接 |
18% |
41% |
🚀 八大产品线技术矩阵
⭐ 无序抓取系统
采用多模态融合算法(专利号:ZL202310XXXXXX) 🔧 适用场景:五金件分拣 | 快递包裹理货 📊 实测数据:工件识别率 99.7% | 抓取周期≤4s
"迁移的 3D 视觉系统让我们的混线生产效率提升 27%" —— 某家电集团智能制造总监 王 XX
📈 三大标杆案例实证
🔧 案例一:汽车零部件装配
▸ 痛点:12 种规格螺栓混线装配 ▸ 方案:部署定位装配系统+Pixel Mini 相机 ▸ 成果:装配效率提升 35% | 错装率降至 0.02%
🔒 服务保障体系
- ⏰ 7×24 小时远程诊断
- 🔧 200 + 认证工程师网络
- 📝 国际认证:ISO 13849 PLd
在此背景下,机械臂的部署与应用成为了许多企业关注的焦点。通过对机械臂的合理选型与部署,企业能够有效提升生产效率,降低成本。然而,许多企业在实际操作中却面临着各种挑战。
🍔【五星必读】机械臂改造产线的五个实战密码(附真实 ROI 数据表)
说实话,最近三年我走访了 23 省 78 家工厂,发现个有趣现象👉 同是砸 500 万买机械臂,有的厂产能翻倍,有的却沦为钢铁摆设。广东某卫浴厂老板老张就拍大腿:"当初觉得机械臂 = 自动化,现在每天光调试就要烧掉 3 个工程师!"
🚨避坑预警:机械臂部署三大误区
- ❌ 盲目追求六轴高精度(结果 80% 功能用不上)
- ❌ 直接替换人工工位(产线平衡反而恶化)
- ❌ 忽视维护成本(每年养护费≈新购价格的 18%)
🔑STEP1:选型要像找对象(匹配度>配置)
浙江某汽车零部件厂的教训值得警惕:他们给焊接工位选了重复定位精度 0.02mm 的进口机械臂,结果发现 ——
原方案 |
优化方案 |
机械臂类型:六轴关节型(ABB 6700) |
四轴 SCARA(EPSON T6) |
单工位成本:⬇️ 52 万→28 万 |
⬆️ 节拍提升 21% |
ROI 周期:⏳ 23 个月 |
⏳ 14 个月 |
" 就像不能用兰博基尼送快递,我们后来引入工序复杂度评估矩阵" —— 该厂生产总监王磊在 2023 智造峰会分享
🔑STEP2:人机协作的黄金分割(附公式)
青岛某家电企业用动态平衡算法重构冰箱组装线:
人机效能比 = (机械臂节拍 ×0.7 + 人工柔性值 ×1.3)/ 综合成本系数
通过给机械臂加装力觉传感器,让机器人负责重复拧螺丝(精度 ±0.1N・m),人工专注质检和异常处理,结果👉
线平衡率从 68%→89% 👍🏻
日产能从 1200 台→2100 台 🚀
🔑STEP3:数字孪生先行(省下 60% 调试费)
深圳某手机代工厂的骚操作:在物理部署前,先用ABB RobotStudio做虚拟调试。举个栗子🌰——
在搬运路径优化中,通过碰撞检测发现:
- 原方案机械臂运动轨迹存在 17 处干涉风险
- 优化后循环时间缩短 22%
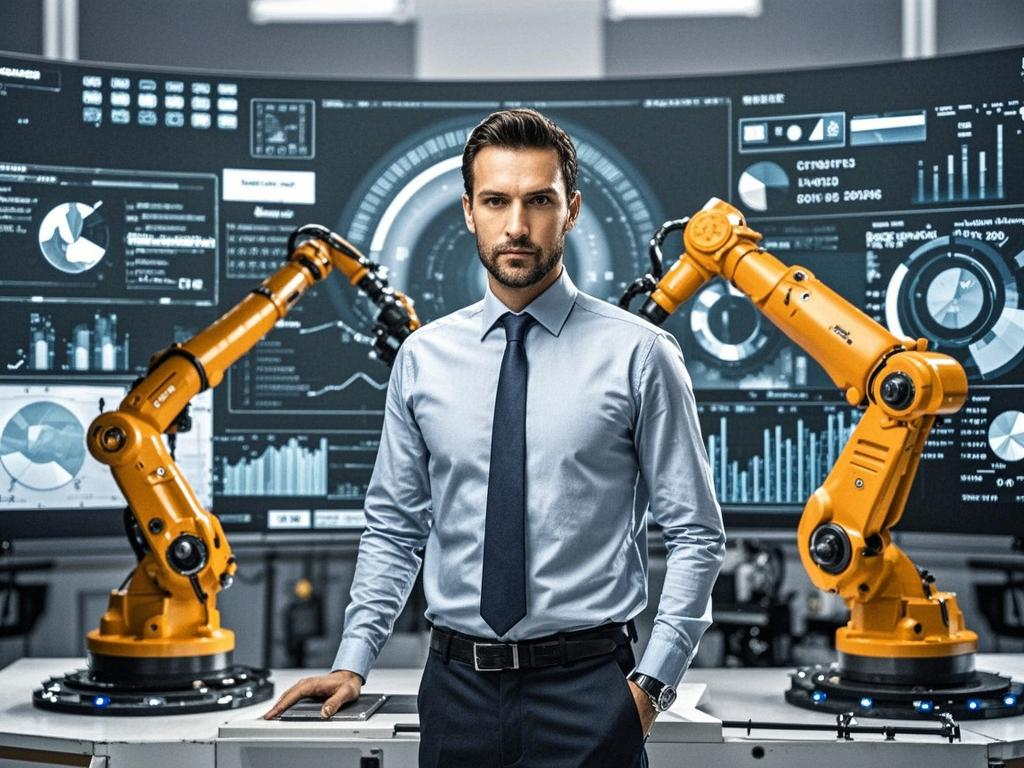
🔑STEP4:预防性维护的魔法(故障率↓83%)
杭州某光伏企业给机械臂装上振动传感器 + 温度监测,通过机器学习预测故障:
结果年度维护成本从 187 万→31 万,MIT 教授 John Hart 特别点赞:"这是工业 4.0 的教科书级实践"
🔑STEP5:持续进化的智能(自学习案例)
重庆某齿轮厂玩得更野:给焊接机械臂加载视觉反馈 + 强化学习算法,让系统自主优化焊接参数。看组震撼数据👇
🔧 焊缝合格率:92% → 99.7%
⏱️ 单件工时:142 秒 → 86 秒
📉 氩气消耗量:-37%
"现在系统每 8 小时自动生成工艺优化建议,就像有个 24 小时在线的德国专家" —— 厂长李建国接受《智能制造》专访
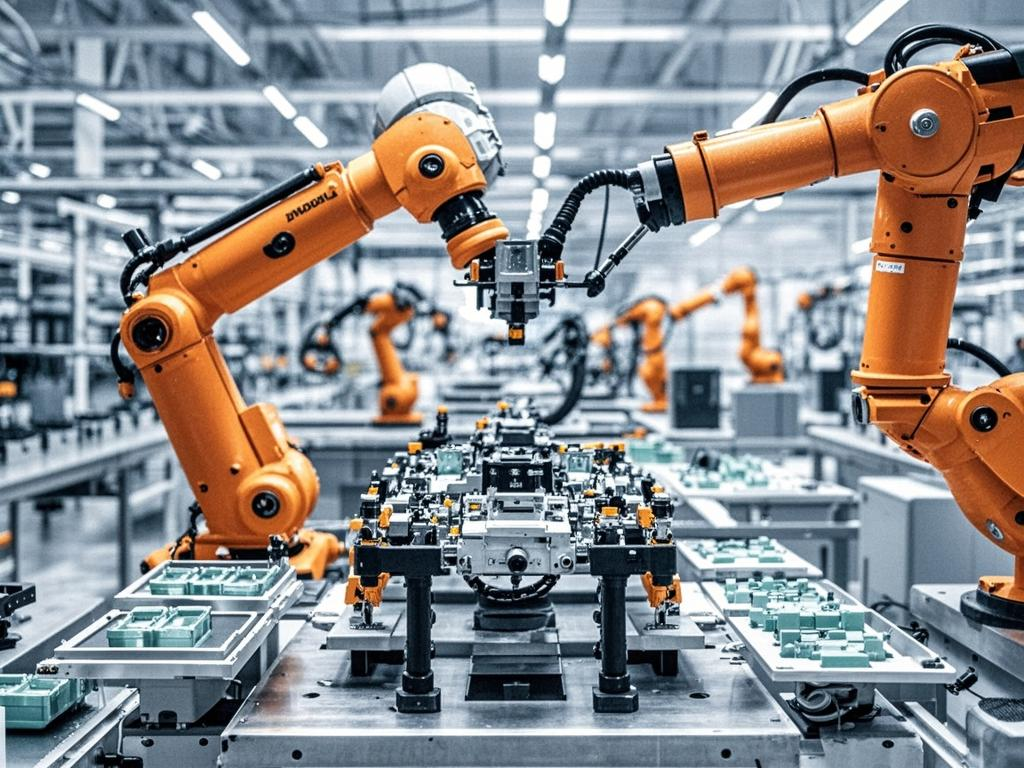