引言:在当今工业生产智能化浪潮中,机器视觉检测凭借其卓越的性能,正成为众多企业提升生产效率与产品质量的关键技术。机器视觉检测相关长尾词如“高精度机器视觉检测”“智能机器视觉检测系统”等也备受关注。它利用光学成像、图像采集与深度学习算法,实现对产品的快速、准确检测。相较于传统人工检测,机器视觉检测优势显著,在工业各领域广泛应用。本文将深入解析其核心优势,盘点应用场景,并提供企业实施解决方案。
一、机器视觉检测技术原理
(一)光学成像与图像采集基础
机器视觉检测首先依赖于光学成像系统,这一系统犹如人类的眼睛,负责捕捉被检测物体的图像信息。它主要由光源、镜头、相机等组件构成。光源为成像提供必要的光照条件,不同的检测需求需要选择不同类型的光源,如环形光源适用于表面平整物体的检测,同轴光源则更适合反光较强物体的检测。
镜头在其中起到聚焦成像的作用,它决定了图像的清晰度和分辨率。优质的镜头能够有效减少像差,确保采集到的图像准确反映物体的真实形态。而相机则是将光学图像转换为数字图像的关键设备,根据不同的应用场景,可选择面阵相机或线阵相机。面阵相机适用于一般的二维平面检测,线阵相机则常用于高速、高精度的一维检测,如在印刷品的检测中,线阵相机能快速检测出印刷图案的缺陷。
例如,在某汽车零部件生产厂的检测环节,通过采用特殊设计的环形光源,结合高分辨率镜头与面阵相机,能够清晰捕捉到零部件表面的细微划痕和瑕疵,为后续的缺陷分析提供了准确的图像数据。
(二)深度学习算法驱动智能识别
采集到的图像数据只是原始信息,要实现对物体的准确检测与分类,还需借助深度学习算法。深度学习算法就如同人类的大脑,能够对大量的图像数据进行学习和分析。
在机器视觉检测中,常用的深度学习算法如卷积神经网络(CNN),它通过卷积层、池化层和全连接层等结构,自动提取图像中的特征信息。以图像中的缺陷检测为例,CNN可以学习到正常产品与缺陷产品在纹理、形状等方面的特征差异,从而准确判断产品是否存在缺陷。
谷歌的工程师曾提到,深度学习算法在图像识别领域的突破,为机器视觉检测带来了质的飞跃。通过对海量数据的训练,模型的识别准确率不断提高。例如,在某电子元件检测项目中,经过深度学习算法训练的模型,对元件表面微小缺陷的识别准确率达到了99%以上,远超传统算法的检测精度。
深度学习算法还具有强大的自适应性,能够不断学习新的样本数据,优化自身的识别能力。当生产线上出现新的产品型号或缺陷类型时,只需向模型中添加相应的样本数据进行再训练,模型就能快速适应新的检测需求。
(三)与传统人工检测的精度对比
传统人工检测主要依靠工人的肉眼和经验来判断产品是否合格。然而,人工检测存在诸多局限性。首先,人的视觉疲劳会随着工作时间的增加而加剧,在长时间的检测工作后,检测精度会大幅下降。据相关研究表明,人工连续工作2小时后,检测准确率会从初始的95%降至85%左右,4小时后可能会降至80%以下。
其次,不同工人之间的检测标准存在差异,即使是经过统一培训的工人,在对产品缺陷的判断上也可能出现分歧。这就导致产品质量的一致性难以保证。
而机器视觉检测则具有高度的稳定性和准确性。它不受外界因素干扰,只要设定好检测标准和参数,就能始终如一地按照标准进行检测。在对某批次食品包装完整性检测中,机器视觉检测系统的准确率达到了99.8%,而人工检测的准确率仅为90%左右。由此可见,机器视觉检测在精度上远远高于传统人工检测,能够为企业提供更加可靠的产品质量保障。
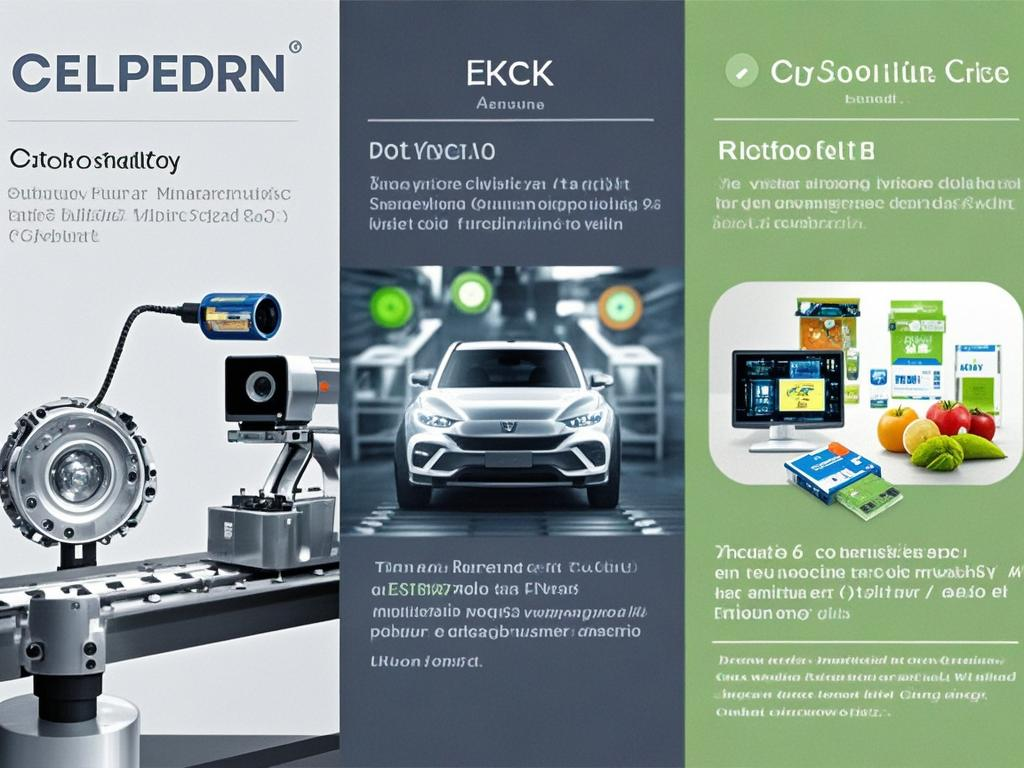
二、工业领域典型应用场景
(一)汽车零部件表面缺陷检测
汽车行业对零部件的质量要求极高,任何细微的表面缺陷都可能影响整车的性能和安全性。在汽车零部件生产过程中,机器视觉检测技术发挥着重要作用。
以汽车发动机缸体为例,其表面的砂眼、气孔等缺陷若未被及时检测出来,可能会导致发动机在运行过程中出现泄漏等严重问题。通过机器视觉检测系统,利用高分辨率相机和特殊光源,能够清晰捕捉缸体表面的每一个细节。结合深度学习算法,系统可以准确识别出各种表面缺陷,并对缺陷的大小、位置等信息进行精确测量。
某知名汽车制造企业采用机器视觉检测系统后,发动机缸体的缺陷检测准确率从原来人工检测的85%提高到了98%。同时,检测效率也大幅提升,从原来每小时检测50个缸体,提高到每小时检测200个缸体,有效降低了企业的生产成本,提高了产品质量。
(二)电子元件尺寸精度测量
电子元件的尺寸精度直接影响到电子产品的性能和稳定性。在电子元件生产过程中,对尺寸精度的要求往往达到微米甚至纳米级别。机器视觉检测技术凭借其高精度的测量能力,成为电子元件尺寸精度测量的首选方法。
例如,在芯片制造过程中,芯片引脚的间距、长度等尺寸参数必须严格控制在规定范围内。机器视觉检测系统通过高倍率的光学镜头和高精度的相机,能够对芯片引脚进行精确成像。然后,利用图像处理算法对图像进行分析,精确测量出引脚的各项尺寸参数。
某电子元件生产企业引入机器视觉检测系统后,元件尺寸精度的测量误差从原来的±5μm降低到了±1μm,大大提高了产品的良品率。同时,由于机器视觉检测系统的自动化程度高,能够实现对大量元件的快速测量,生产效率提高了3倍以上。
(三)食品包装完整性质检
食品包装的完整性对于保障食品的质量安全至关重要。在食品生产线上,机器视觉检测系统可以快速检测食品包装是否存在破损、封口不严等问题。
例如,在某饼干生产企业,通过在包装生产线末端安装机器视觉检测系统,利用特殊的光源和相机,能够清晰拍摄到饼干包装的各个部位。系统采用深度学习算法对图像进行分析,能够准确识别出包装是否存在破损、褶皱以及封口处是否密封良好等情况。
自从引入该机器视觉检测系统后,该企业食品包装的缺陷检出率从原来人工检测的80%提高到了95%以上,有效减少了因包装问题导致的食品变质和召回事件,保障了消费者的权益,提升了企业的品牌形象。
三、企业实施解决方案
(一)生产线改造需求诊断要点
-
产品特性分析:企业首先需要对自身生产的产品进行详细分析,包括产品的材质、形状、尺寸、表面特性等。不同的产品特性决定了机器视觉检测系统的选型和配置。例如,对于表面反光较强的产品,需要选择特殊的光源和相机,以避免反光对检测结果的影响。
-
生产工艺了解:深入了解生产工艺流程,明确在哪些环节需要引入机器视觉检测技术。不同的生产环节对检测的要求不同,如在装配环节,可能更注重零部件的装配位置是否准确;在成品检测环节,则更关注产品的外观缺陷和整体性能。
-
检测精度与速度要求确定:根据产品质量标准和生产效率要求,确定机器视觉检测系统的检测精度和检测速度。如果对产品的尺寸精度要求极高,就需要选择高精度的相机和镜头;如果生产线上产品的流动速度较快,就需要选择检测速度快的系统,以确保不影响生产效率。
(二)视觉系统硬件选型指南
-
相机选型:根据检测精度要求,选择合适分辨率的相机。一般来说,检测精度越高,所需相机的分辨率也越高。同时,要考虑相机的帧率,以满足生产线的检测速度要求。例如,对于高速生产线,应选择帧率较高的相机。另外,还需根据检测环境选择合适的相机类型,如在高温、潮湿等特殊环境下,需选择具有相应防护等级的相机。
-
镜头选型:镜头的焦距、光圈等参数直接影响成像质量。根据被检测物体的大小和检测距离,选择合适焦距的镜头。例如,对于近距离检测小物体,应选择短焦距镜头;对于远距离检测大物体,则需选择长焦距镜头。同时,要注意镜头的畸变程度,尽量选择畸变较小的镜头,以保证检测的准确性。
-
光源选型:光源的类型和光照方式对检测结果影响很大。常见的光源类型有环形光源、背光源、同轴光源等。根据被检测物体的表面特性和检测目的,选择合适的光源。如检测透明物体时,背光源是较好的选择;检测表面不平整物体时,环形光源可能更合适。
(三)检测算法定制开发流程
-
数据采集:首先需要收集大量与被检测产品相关的图像数据,包括正常产品和各种缺陷产品的图像。这些数据将作为训练模型的基础,数据的质量和数量直接影响算法的性能。数据采集过程中,要确保图像的真实性和多样性,涵盖不同生产批次、不同环境下的产品图像。
-
数据标注:对采集到的图像数据进行标注,明确图像中每个物体或缺陷的类别、位置等信息。标注工作通常由专业的标注人员完成,标注的准确性至关重要。为了提高标注效率,可以采用一些自动化标注工具辅助标注。
-
算法选择与训练:根据检测任务的特点,选择合适的深度学习算法,如卷积神经网络(CNN)中的ResNet、YOLO等。然后使用标注好的数据对选定的算法进行训练,通过不断调整算法的参数,使模型能够准确识别出产品中的各种缺陷和特征。训练过程中,要注意防止模型过拟合,可采用数据增强、正则化等方法提高模型的泛化能力。
-
模型评估与优化:训练完成后,使用一部分未参与训练的测试数据对模型进行评估,计算模型的准确率、召回率等指标。根据评估结果,对模型进行优化,如调整算法结构、增加训练数据等,直到模型达到满意的性能指标。
-
部署与应用:将优化后的模型部署到机器视觉检测系统中,进行实际生产环境的测试和应用。在应用过程中,持续收集新的图像数据,对模型进行实时更新和优化,以适应生产过程中可能出现的产品变化和新的缺陷类型。
版权声明:本文内容由网络用户投稿,版权归原作者所有,本站不拥有其著作权,亦不承担相应法律责任。如果您发现本站中有涉嫌抄袭或描述失实的内容,请联系我们jiasou666@gmail.com 处理,核实后本网站将在24小时内删除侵权内容。